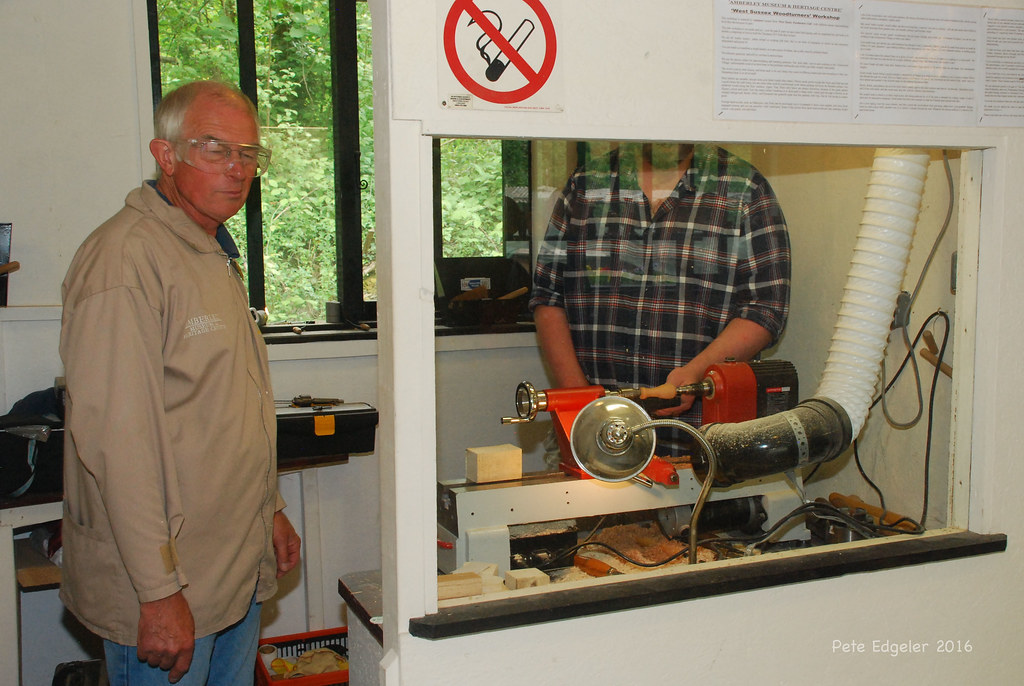
To compensate for awkwardly placed fingers, adjust the angle of the top bars if the lathe does lack a proper tool rest. You can glide your fingers back and forth with many tool rests that have flat spots. Some are adjustable and fit most lathes, while others have multiple height settings. These are the important things to look at when purchasing a tool rest for your Lathe.
Light source
If you don't know what a light source is for a toolrest on a lathe you are not alone. Many lathes come with overhead lighting as well as fixtures that attach to the ceiling or headstock. These lights offer additional lighting, but can block operator access. A tool rest with an integrated light source will be the best choice for larger lathes.
A tool rest to be used with a lathe has a horizontal arm as well as a vertical support. On the tool arm's front side, mount a light source. Preferably an LED illumination strip. The strip is attached to an electrical power source by means of a wire 20. Alternately, the tool rest can be used without a source of light. This invention will allow the creation of a better tool rest for lathes that incorporate a light source.
Support element
Support element for tool rest lathe addresses a variety of issues related to unanticipated movement of the toolrest. The prior art supports the toolrest with a point to point abutting arrangement. The toolrest must support torque and axial force when tooling. Therefore, the friction force generated cannot be used to support the rest. This design raises safety concerns. The support element for tool rest on lathe is used to protect the toolrest against torque and axial pressure generated during tooling.
In most cases, a toolrest for a lathe comprises an up-standing bar. The bar acts as a restraint, and can have grooves or sleeves for finding the tool. Some models have a handle to guide the tool while turning. These toolrests may be made from metal or wood. You should smoothen wooden toolrests. If you don't have the budget for a support component for your tool rest for lathe, you can still choose a wooden one.
Adaptive device
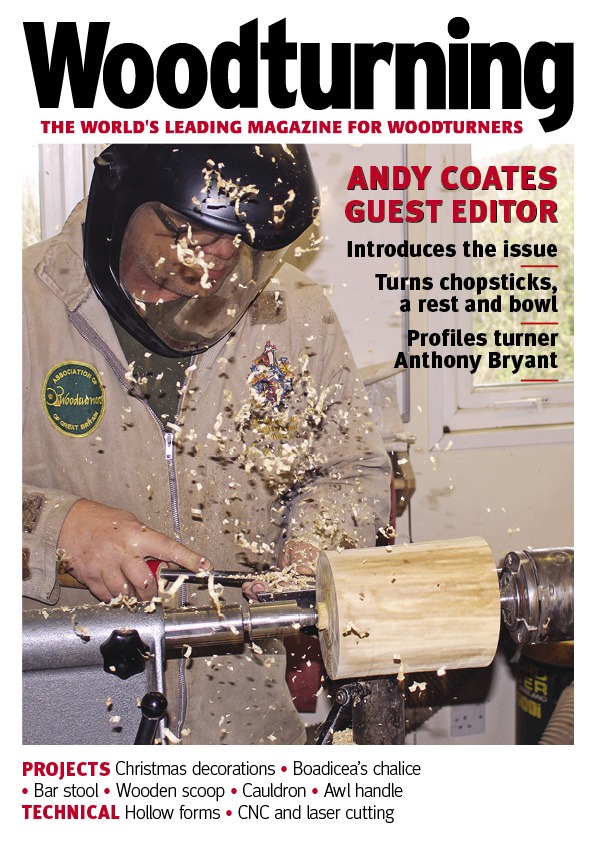
The adaptive device 100 is an externally cylindrical sleeve with a head and threaded section. There's also a threaded portion on the outer edge that connects to an opening 150. A portion of the shoulder 140 has been milled and forms a flat 160 for the set screws 370 to be inserted into the lathe-holder 310. The set screws370 press against flat surface 160 to keep the adaptive device positioned within the lathe.
The Mortimer pin rest claims a gated function, but the support bar rides virtually parallel to the tool shaft, so it should provide sufficient levering ability sideways. However, the gate of this device is exceptionally wide, which almost certainly suffers from cam locking. This is a significant improvement on a standard tool rest but it does not offer much in the way of motion restriction or fine tool control. It is not recommended for users who require precise tool control but want to have complete tool control.
Cutting tool
If you are new to lathe work, the first thing you'll want to consider is purchasing a cutting tool rest for your lathe. This accessory will allow you to support your tool as close to the wood as possible while it rotates. The body of a toolrest slopes backward from its forward edge. This helps to position your tool at the optimal angle to cut. With a file, you can finish the surface of the cutting tool rest to ensure a smooth working surface.
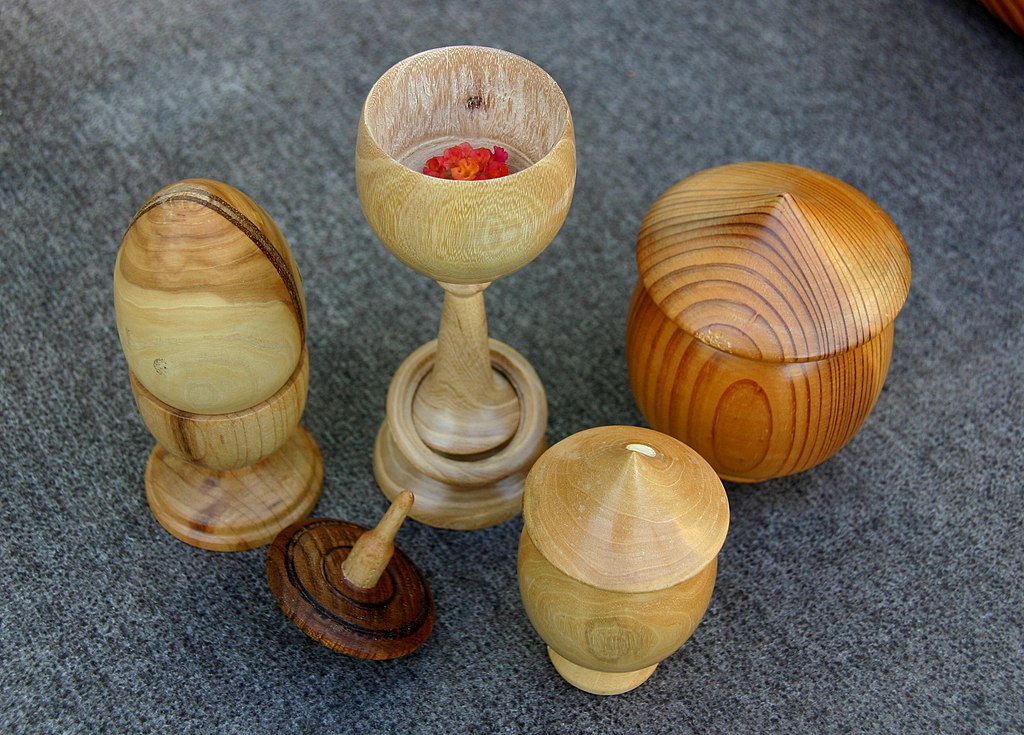
For your lathe's cutting tool rest, make sure to look for one with flat spots. This will keep your fingers from scratching the surface. This tool rest prevents your hands from sliding off the cutting instrument. It is also useful for keeping the workpiece stable during high-speed turning. There are many sizes that will fit your lathe. If you are unsure, ask a professional to help you make a selection.
FAQ
How long does it take to finish a piece of furniture?
It all depends on what type of wood you use, how complex your design is, and how much finishing you use. Hardwoods, for example, require more maintenance than softwoods. Hardwoods tend to be more expensive that softwoods. But they last longer and resist moisture better. It takes between one and three months to finish a piece.
What woods are suitable for making furniture?
Woods are classified by their hardness. Softwoods can be pine, fir or cedar. Because they are resistant to rot, softwoods are often used as outdoor furniture. The hardwoods are oak, maple and mahogany. They are generally indoors as they don't weather well outside.
What tools should you start with to become a woodworker
Woodworking is an art. It requires patience. It takes time for you to master the different techniques and tools that are required to woodwork.
There are many types of woodworking equipment on the market today. Some people prefer to use power tools while others prefer manual tools.
It's your choice. But you should ensure that you pick the right tool. You might start with a simple set of tools if you don't have much experience.
A router is a tool that cuts intricate shapes in wood. You can also learn how to use it. These tools can be purchased at most hardware stores.
How much money will I need to get started?
Because each project is unique there are no exact numbers. Here are some factors to help you estimate how much money you will need.
-
Material costs
-
Tools and equipment
-
Time spent working on this project
-
Hourly rate
-
What profit are you expecting to earn?
-
Hire help
If you're just starting out, you may decide to start small by making simple items such as boxes and picture frames. You will gain more experience and be able to tackle larger projects.
What is the main difference between plywood or particle board?
Plywood can be described as a mixture of layers and wood that have been pressed together with pressure. Plywood can come in many thicknesses and is used for flooring and cabinets. Particle board is made from sawdust mixed with resin and then compressed into large blocks. It's often used for home renovation projects. Both types of boards are durable and easy to cut.
Statistics
- Most woodworkers agree that lumber moisture needs to be under 10% for building furniture. (woodandshop.com)
- In 2014, there were just over 237,000 jobs for all woodworkers, with other wood product manufacturing employing 23 percent; wood kitchen cabinets and countertop manufacturing employing 21 percent. (theartcareerproject.com)
- Woodworkers on the lower end of that spectrum, the bottom 10% to be exact, make roughly $24,000 a year, while the top 10% makes $108,000. (zippia.com)
- Average lumber prices rose about 600 percent between April 2020 and May 2021. (familyhandyman.com)
External Links
How To
How to make wood joints
This tutorial will show you how to join two pieces of wood together. We'll use the "pocket hole joint," which means we drill holes in the wood and then glue them together. This method is great if your wood's straight and smooth. Try dowel joinery instead if your wood doesn't look straight. These are the steps
-
Drill Pocket Hole Joints. You will need to measure and mark the exact location of your pocket hole joint. Next, drill 3/4 inch holes in each end of each piece using a handheld drilling machine or jigsaw.
-
Sand Smooth. Sanding the edges of the wood will help to prevent the joint from splitting later.
-
Glue the two sides of the wood together. Apply glue to both the ends of the wood. Allow it to cool for at least 5 minutes before you attach the pieces.
-
Secure the pieces together. After the glue has dried you can attach the pieces to form a flush joint.
-
Trim Joinery. Trim any excess wood surrounding the joint once the glue has dried completely.
You should leave enough space between the pieces to allow you to turn them inside-out.